
A6061-RAM2 sets significant milestone; NASA to share RAMFIRE data and process with commercial stakeholders and academia.
NASA continues to add to the United States’ ability to reimagine the future of rocket engine technology by accelerating the advancement of lightweight rocket nozzle production with unconventional means. The recent successful conclusion of NASA’s Reactive Additive Manufacturing for the Fourth Industrial Revolution (RAMFIRE) project has established the viability of additive manufacturing (AM) aluminum rocket nozzles with A6061-RAM2 powder.
The completion of multiple aluminum nozzle hot-fire tests is a giant leap in space travel, but equally important is the data collected. The significance of interjecting the knowledge and experience gained from NASA’s funding and the successful collaboration with other partners in the ACO RAMFIRE project will certainly influence future AM innovations beyond rocket propulsion.
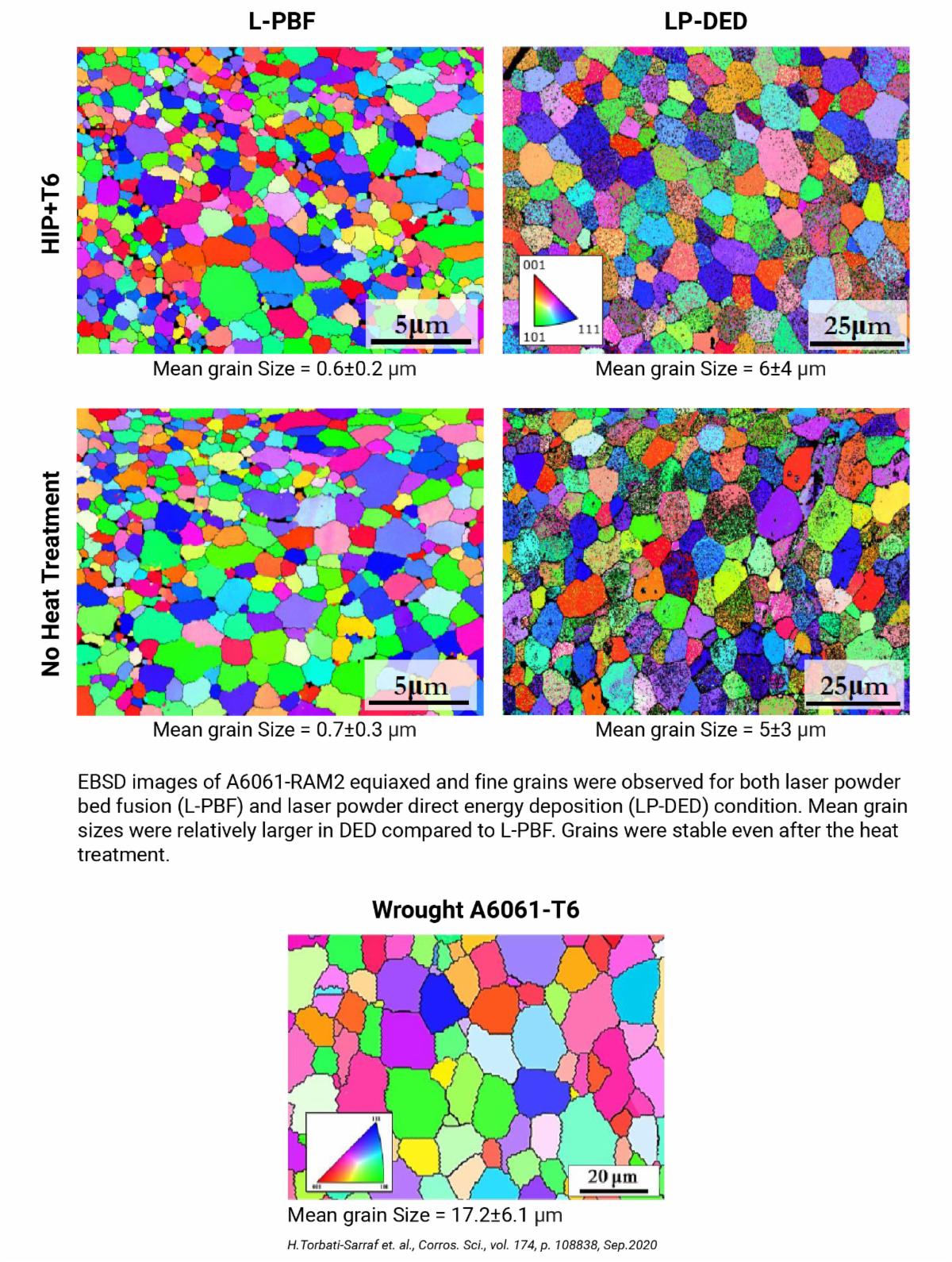
Elementum 3D was honored to be a part of the RAMFIRE project. Having the opportunity to work closely with NASA engineers and scientists and RPM Innovations made for early successes in the development of an aluminum material feedstock capable of printing in a large blown powder DED format. Although the final demonstration was an actual hot-fire tests of the rocket nozzle with liquid hydrogen/liquid oxygen and liquid methane/liquid oxygen, the scope of the project also included microstructure analysis (EBSD, BSE, EDS), tensile behavior at different temperatures (-195 °C, 21 °C, 100 °C, 200°C, 300 °C, 400 °C), and fatigue behavior at different temperatures (-195 °C, 21 °C, 100 °C, 200°C). Showing that the thermal and mechanical properties of A6061-RAM2 can be used to design a regeneratively cooled rocket nozzle using blown powder DED additive manufacturing brings incredible confidence to this material and its versatility.
The research data acquired from the optimization of A6061-RAM2 aluminum alloy for large blown powder DED will inspire commercial space companies and organizations outside of aerospace to view additive manufacturing as an effective option to elevate application performance, reduce part complexity costs, and encourage part consolidation. Ultimately, NASA’s long-term goal is to cultivate innovative technologies, such as AM, and collaborate with other industries to make the resulting data and expertise available to all AM enthusiasts.

- Everything You Need To Know About Cold Metal Fusion
- The future of automotive manufacturing: adding additive
- Additive Manufacturing Strategies 2024: Choose Your Own Adventure
- 3D printing promises more efficient ways to make custom explosives and rocket propellants
- White House Announces AM Forward Fund at Convening of Small Business Leaders
- Authentise awarded 3 grants to advance 3D printing lattices, measurement and remanufacturing projects
- Trumpf and Elementum 3D help redesign Intense Cycles’ classic M1 downhill race bike
- AI accelerates process design for 3D printing metal alloys
- Tackling the Challenges of Manufacturing for Harsh Environments
- AM in 2024: The 3D printing trends and applications you need to know about
- Additive Talks | New Space & AM: Current Applications driving industrialization & technological challenges
- Pittsburgh, The New Home of 3D-Printed Steel