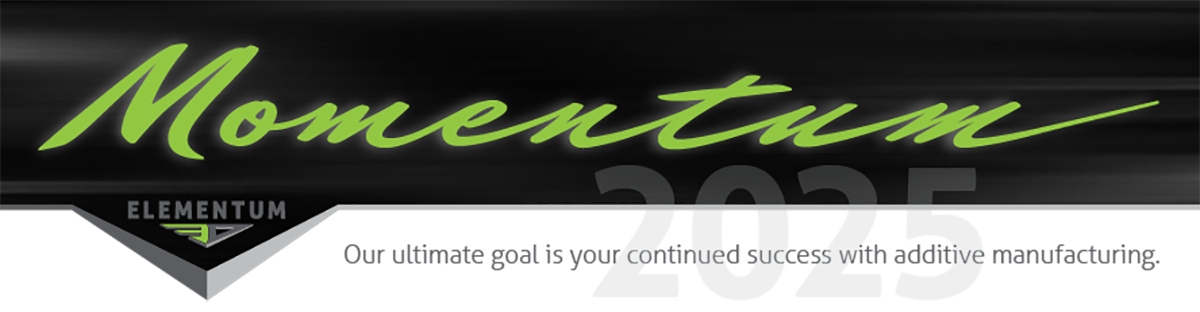
May 2025
NASA Webinar Features Elementum 3D On Thursday, May 8, 2025, Elementum 3D’s Chief Technical Officer, Dr. Jeremy Iten, shared the company’s journey from startup to industry leader in additive manufacturing
NASA Webinar Features Elementum 3D On Thursday, May 8, 2025, Elementum 3D’s Chief Technical Officer, Dr. Jeremy Iten, shared the company’s journey from startup to industry leader in additive manufacturing
Elementum 3D Included in $46B US Air Force Contract Elementum 3D has been chosen by the U.S. Air Force to be included in the Enterprise-Wide Agile Acquisition Contract (EWAAC) indefinite
Elementum 3D Supports NASA HUNCH Program It has been months since NASA launched the Lunar Additive Manufacturing project through its HUNCH program and the competitors list is down to six high schools.
Elementum 3D Awarded AFWERX Contract for Permeable Additive Manufacturing Elementum 3D has been selected by AFWERX, the innovation arm of the Department of the Air Force (DAF), for a SBIR
2024 breakthroughs and highlights Elementum 3D’s first steps into 2025 have directly benefited from the momentum built throughout 2024. Last year saw substantial progress on many initiatives and company-wide achievements
Elementum 3D and Höganäs announce powder distribution agreement at Formnext This year’s Formnext was extra special, it proved again to be the best place to connect with the global AM
Elementum 3D first to commercialize NASA’s breakthrough high-temp AM superalloy GRX-810 Elementum m 3D is pleased to announce the official commercial release of GRX-810. This printable nickel cobalt chromium oxide
Elementum 3D’s A6061-RAM2 makes Space flight history with NASA JPL’s Jupiter ice moon exploration Congratulations to NASA’s Jet Propulsion Laboratory (JPL) on a successful Europa Clipper launch. This is a monumental
Elementum 3D Celebrates 10 Years of AM Materials Innovation This October, Elementum 3D proudly celebrates 10 years in business and the ongoing commitment to push the limits of what is
Elementum 3D helps advance rocket propulsion applications Elementum 3D is honored to align with the Rapid Analysis and Manufacturing Propulsion Technology (RAMPT) project, a public-private partnership led by NASA. The
Air Force RSO expands A6061-RAM2 testing Agreement The United States Air Force Rapid Sustainment Office (RSO) recently expanded their material characterization agreement with Elementum 3D (E3D) focused on specification, dataset
Materials Consortium event “Unlocking Key Materials in Metal 3D Printing” is a success! On June 24th, the Materials Consortium (MC) hosted its first event at the Mimo Technik Facility in
A7050-RAM2 receives Aluminum Association registration Elementum 3D, a leading developer and supplier of metal additive manufacturing (AM) advanced materials, print parameters, and services proudly announces the registration of its second
Will the successes of NASA’s RAMFIRE project lead to an operational aerospike engine? In addition to the February 2024 Momentum article, which established the viability of additive manufacturing (AM) aluminum
Purdue University Space Program students select A6061-RAM2 for their TADPOLE propulsion system Additive manufacturing (AM) is transforming the impossible into possible. It’s also transforming how the next generation of innovators
A6061-RAM2 sets significant milestone; NASA to share RAMFIRE data and process with commercial stakeholders and academia. NASA continues to add to the United States’ ability to reimagine the future of
America Makes Selects Elementum 3D to Lead “Proliferation of AM Aluminum Alloy Material Datasets” Team Elementum 3D awarded $2,875,000 to expand availability of statistically based industrially relevant AM material. Elementum
Elementum 3D’s AM materials product line expands to include a ductile, high-strength aluminum alloy that eliminates the need for heat treatment Elementum 3D is excited to announce the expansion of
U.S. Army leverages Elementum 3D technology Back in September 2023, we informed our readers about the U.S. Army Futures Command (AFC) awarding Elementum 3D a Phase II SBIR contract. Well,
TAE’s Plasma Generator system optimized with the power of AM The benefits of additive manufacturing (AM) are attractive to many manufacturers, and TAE is one manufacturer taking advantage of these
U.S. Army leverages Elementum 3D technology for future readiness Elementum 3D was recently awarded a Phase II SBIR contract with the U.S. Army Futures Command (AFC) to develop high-strength aluminum
RAM technology is solving the Navy’s need for a reliable AM-ready high temperature material As of August 2023, Elementum 3D is halfway through a two-year Phase II SBIR project funded
Elementum 3D to lead project focused on modeling additive geometries with novel materials for aerospace applications Elementum 3D (E3D) was recently awarded $500,000 in funding through the America Makes Cooperative
JPL qualifies Elementum 3D A6061-RAM2™ material for flight hardware production The quest for new materials for use in space exploration has found success in additive manufacturing. On April 21, 2021,
Pure copper properties improved To achieve cutting edge performance, there is a constant need for advancements that push the boundaries of technology. Through rigorous materials engineering of our commercially pure
Elementum 3D launches new high-strength aluminum alloy that eliminates the need for heat treatment Elementum 3D, is set to launch its revolutionary A5083-RAM5 aluminum alloy at the upcoming Rapid +
IN625-RAM2 Optimized Parameters for Unparalleled Speed Elementum 3D is excited to announce the pilot release of a new high-speed printing parameter set for our IN625-RAM2 enhanced nickel superalloy. Our team
Momentum builds We have set many lofty yet achievable internal and external goals for 2023 and are pleased to report that our team has already secured more purchase orders and
A2024-RAM2 fatigue properties are examined for industrial production qualification The recent Science Direct article titled “Microstructure and Fatigue Properties of Al2024-RAM2 Aluminum Alloy Obtained by Laser Powder Bed Fusion” disseminates their fatigue
Wrapping up 2022 with two in-depth video podcasts Video Podcast #1 AM Voices chats with our Founder and President of Elementum3D, Dr Jacob Nuechterlein and Director of Business Development,
Materials science and metallurgy experts helping you redefine what’s possible.
Copyright © 2024 Elementum – All rights reserved
Patrick Callard earned a B.B.A. in advertising from Western Michigan University in 1990. He provides over 30 years of experience in marketing communications, new business development and market outreach.
He has managed multiple marketing projects and budgets for a variety of services and products.
Patrick also successfully grew an IT consulting business from a two-man basement business to a profitable eight employee business in 4-years. Patrick’s daily focus is to unify customer experience, brand purpose, creative communication, and marketing technology to drive the growth of the business.
Tyler’s message will key on blown powder Directed Energy Deposition (L-DED) for AM and repair and why this process is being realized by industry as one of the key pillars in printing thin wall part structures and large part envelope requirements.
Shawn will reveal how Lithography-based Ceramic Manufacturing (LCM) is producing high resolution, high performance technical ceramics that can serve a wide range of applications and structural materials, such as alumina, zirconia, and silicon nitride. He will also touch on how LCM has progressed into multi-material components incorporating ceramics and metals.
Jeff’s presentation will focus on the advances in wire DED, including welding processes for wire DED (arc, laser, and e-beam), next-generation alloys for large format metal 3D printing, and use cases that can benefit from replacing large forgings, replacing large machined billets, and producing advanced tooling — enabling next generation designs.
Dr. Jacob Nuechterlein is the founder and president of Elementum 3D in Erie, CO. He earned his Bachelor of Engineering, Master of Science, and Doctor of Philosophy at the Colorado School of Mines. Jacob has been researching, teaching, or consulting on topics such as casting and powder metallurgy for the last 14 years. Elementum 3D’s work with powder bed laser additive manufacturing is based on these principles. In addition, is thesis work in thermodynamics and formation kinetics of metal matrix composites is directly related to all 3D printing processes.