On October 23, 2020, the U.S. Air Force’s inaugural Advanced Manufacturing Olympics (AMO) event Technical Challenges winners were announced. Elementum 3D was selected as the event’s first ever Gold Medalist by winning the “Material Hurdles” challenge with their A7050-RAM2 high-strength aluminum alloy!
The AMO competition, hosted by the USAF Rapid Sustainment Office (RSO), comprised 64 teams competing in five technical challenges for AMO medals and the chance to win up to $100,000. The entrants were each evaluated on their ability to solve some of the U.S. Air Force’s most significant sustainment issues. The Technical Challenges were judged by 25 subject matter experts from academia, the U.S. Military (Air Force, Army, and Navy), the Federal Aviation Administration, Ford, Amazon, and aerospace and defense companies. The four-day virtual event held October 20 through 23, 2020, was filled with compelling speakers, insightful sessions, exciting technology demos, and networking.
Elementum 3D, a developer and supplier of advanced metal additive manufacturing powders and processes, chose their new high-strength A7050-RAM2 powder to compete against eight other aluminum materials finalists in the “Material Hurdles” challenge. “We are honored to have our commercially available high-strength A7050-RAM2 aluminum alloy selected as the AM material to best meet the USAF’s challenge goal of demonstrating advances in AM aluminum material properties to address sustainment of traditionally manufactured 7075 and 7050 aluminum parts,” said Dr. Jacob Nuechterlein, President and founder of Elementum 3D.
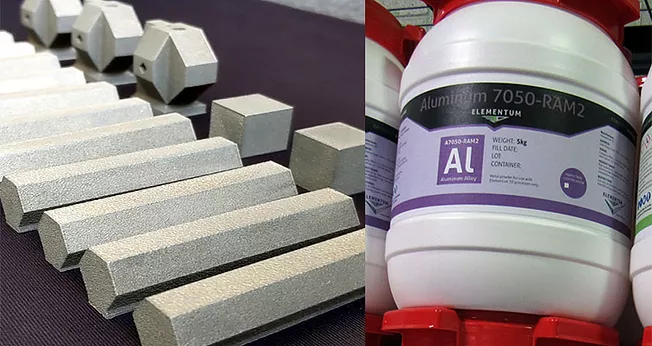
Each team was required to accurately recreate the same 3D printed parts from an existing Technical Data Package using innovative materials and techniques, all while demonstrating accuracy, skill, completeness, ease of use, and speed of production. “We entered our A7050-RAM2 aluminum alloy to deliver on the AMO event’s initiative to obtain a material capable of being 3D printed into components for use in demanding Air Force conditions,” said Dr. Nuechterlein.
The USAF is working to adopt additively manufactured aluminums because of their potential for rapid on-demand production of high strength sustainment parts. Accomplishing this goal also facilitates reduction of component weights and reduced raw material requirements due to improved buy-to-fly ratios. By adopting AM and other forms of advanced manufacturing, the RSO can cut down on sustainment costs which make up 70 percent of the USAF budget. Elementum 3D’s printable A7050-RAM2 feedstock supports these goals by enabling efficient 3D printing of components out of a lightweight and high-strength aluminum material that also offers excellent fatigue life and stress corrosion cracking resistance.
The U.S. Air Force has a long history of fostering innovative solutions and these AM Olympics technical challenges were the latest means in generating transformative opportunities within advanced manufacturing. It sets in motion the USAF’s willingness to embrace leading edge solutions making for a more sustainable Air Force.
Congratulations to all the AMO’s Materials Hurdles Challenge medalists:
Gold: Elementum 3D, Inc.
Silver: University of Waterloo and The Barnes Global Advisors, LLC
Bronze: Castheon, Inc.