
Two SBIR Phase I grants awarded Elementum 3D
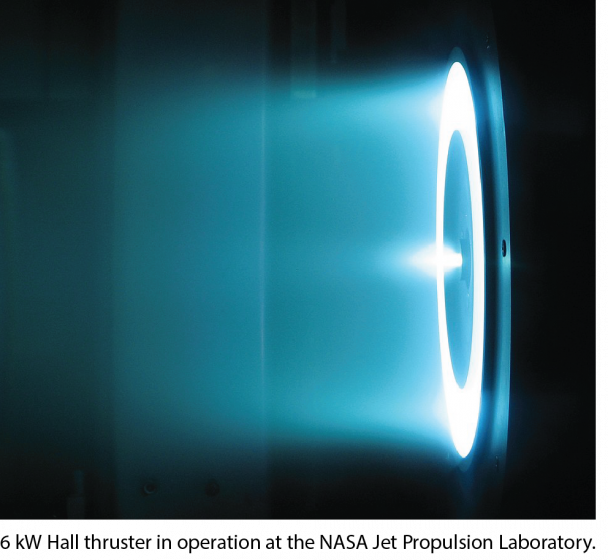
In May 2021, NASA awarded a SBIR Phase I grant to Elementum 3D. The SBIR is centered around the development of additively manufactured soft magnetic materials for large diameter Hall-effect thrusters. In-space electric propulsion systems are of growing importance for interplanetary missions and better manufacturing methods are needed to produce large diameter Hall-effect thrusters with the right magnetic properties and structural robustness.
We are honored to work with NASA and partner Altius Space Machines in developing AM iron-cobalt alloys, printing processes, and post processing to achieve the needed performance for Hall-effect thrusters and other space and terrestrial uses.
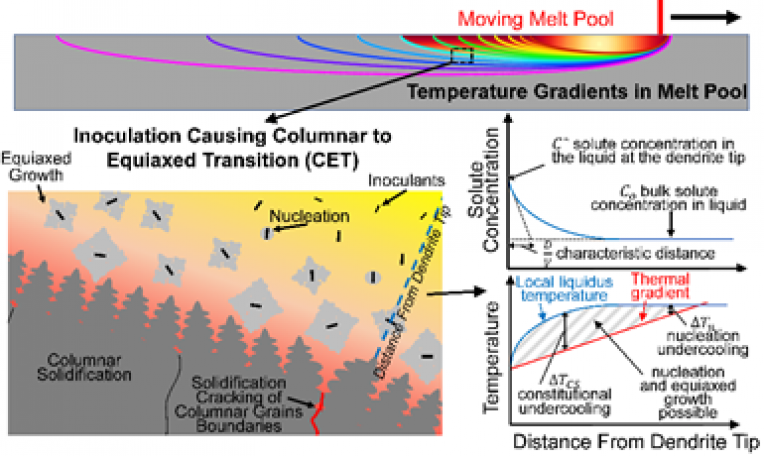
In June 2021, the Department of the Navy awarded Elementum 3D a contract for their Phase I SBIR project “Controlling Microstructure Through Nucleation – The Key to Designing the Next Generation of High-Performance Alloys for Additive Manufacturing”. Working together with Dr. Jonah Klemm-Toole at the Colorado School of Mines and Special Aerospace Services, Elementum 3D will develop a modeling framework linking alloy chemistry, AM processing, thermal history, microstructure and defect development and mechanical properties. Elementum 3D’s rapid experimental alloy development (READ) process will be used to provide extensive experimental validation of the model predictions to allow for iterative model development and improvements. The validated model will then be used as a guide for development of new designed-for-AM nickel superalloys, copper alloys, and more.
Discover how 3D printing steel can achieve ductility with increased strength
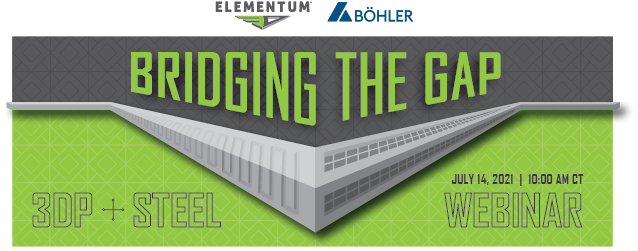
Our expert-led webinar will discuss Elementum 3D’s steel initiative to integrate RAM technologies into Böhler’s high-quality and high-performance steel-based additive manufacturing (AM) alloy powders.The 1.5 hour webinar will explore efforts being made to develop a stronger 3D printed (3DP) laser powder bed fusion steel alloy powder and up-to-date insights on the latest emerging technology trends as they relate to printed steel components with conformal cooling for die casting applications, wear protection layers and tooling. |
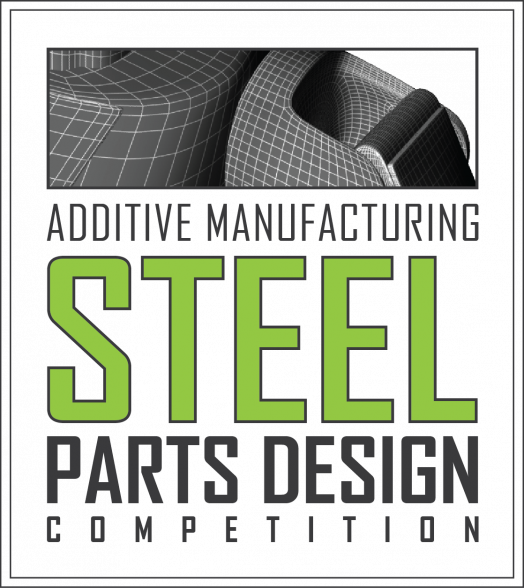
Entrance In AM Steel Part Design Contest Included with Registration!
The webinar also includes the introduction of the “Additive Manufacturing Steel Part Design Competition.”
A panel of judges will review all submitted CAD drawings and will determine the winner based on the collective score from a variety of categories.
Winner will receive complimentary Böhler AMPO steel powder of their choice and print time from Elementum 3D to print up to two iterations of their winning design.
Data sheet updates
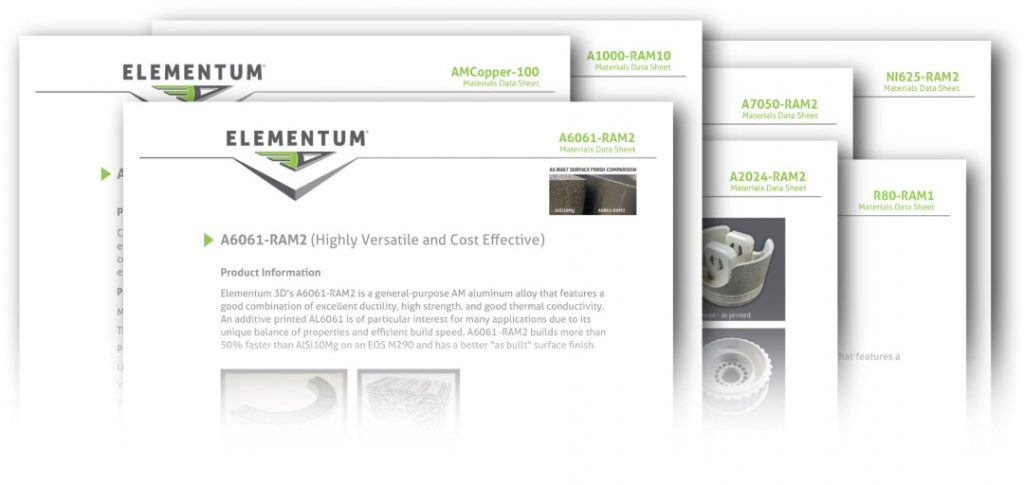
In order to provide the best customer service, we are pleased to announce that we have recently posted updated data sheets. We invite you to visit the Elementum 3D “Data Sheets” web page obtain to the most up-to-date data points and charts.
U.S. Navy high-tech challenge recognizes A6061-RAM2 as metal AM solution
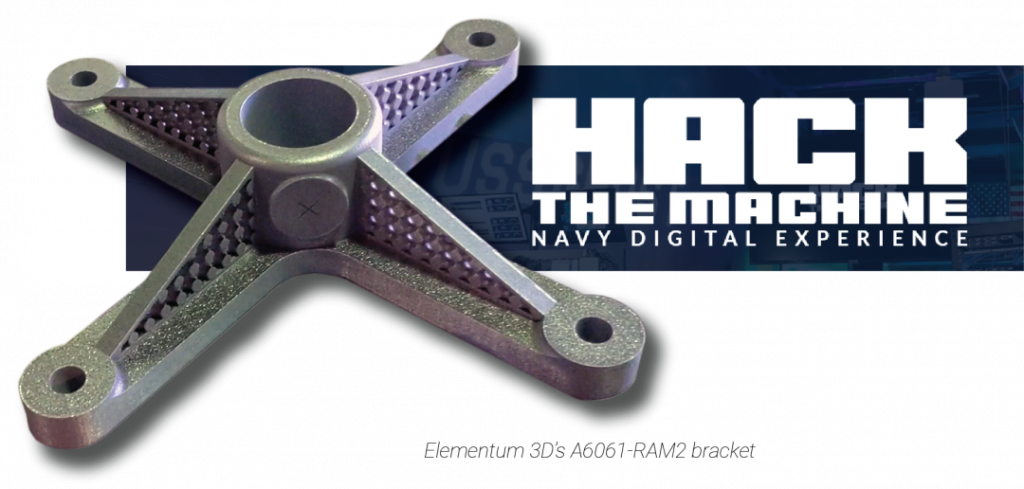
On June 2, 2021, Elementum 3D was an award winner in the “Heavy Metal” track of the Navy’s “HacktheMachine Challenge.” The challenge included hundreds of participants, across the Navy enterprise, as well as those in the public and private sectors. The event’s goal was to solve some of the Navy’s most high-tech challenges in a three-track prize challenge called “HACKtheMACHINE” — hosted by Naval Sea Systems Command (NAVSEA).
Elementum 3D surpassed all other materials development contestants in the “Heavy Metal” track, a hybrid virtual and physical challenge that allows the Navy to tap into a wider and more diverse base of advanced manufacturing in this country and beyond. Elementum 3D’s A6061-RAM2 part was entered in the main Heavy Metal track challenge, entitled “Light It Up,” which consisted of converting an existing 2D drawing of a standard bracket that connects a light fixture to a stanchion into an innovative 3D printed part. The printed bracket was then submitted for evaluation, which included vibration and shock testing.
Innovations created through Heavy Metal track challenge will accelerate the adoption of metal additive manufacturing (AM) in the U.S. Navy and support their initiative of bringing innovative processes and technologies directly those who need it. “At sea, if I have a part fail – I need to be able to print as much of that part as I can while at sea,” said Rear Adm. Jason Lloyd, U.S. Navy, Naval Sea Systems Command, Chief Engineer and Deputy Commander for Ship Design, Integration and Naval Engineering.
Elementum 3D is honored to be acknowledged by the Navy as a leader in the AM community and we look forward to utilizing our technology and expertise to strengthen the Navy by partnering with them to overcoming current and future advanced manufacturing maritime challenges.
Cool Part Show showcases A1000-RAM10
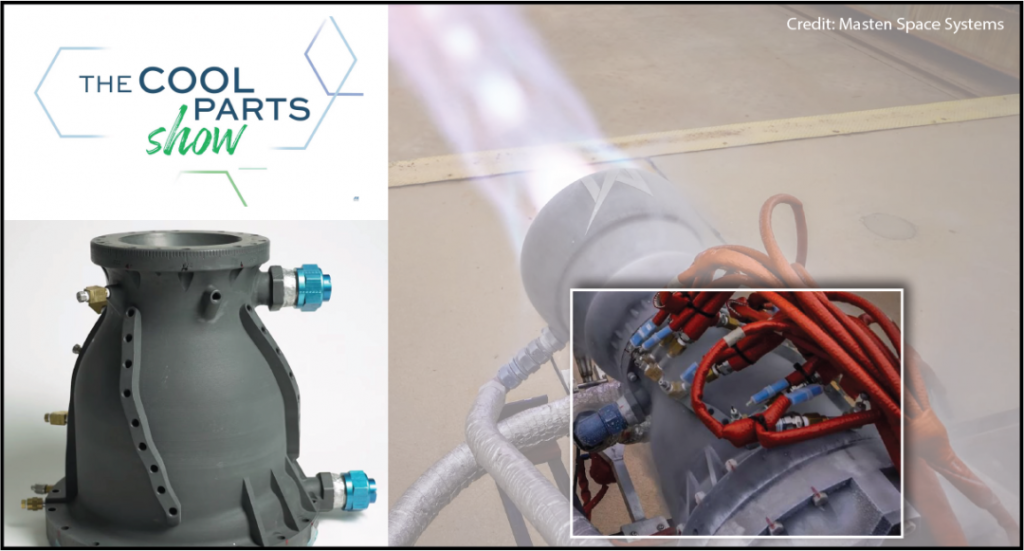
On May 12, 2021, “The Cool Parts Show” broadcasted their 30th episode, “Lightweight Combustion Chamber Part of 3D Printed Rocket Engine.” It featured Masten Space Systems lightweight, reusable combustion chamber design for NASA’s “Broadsword” rocket engine printed by Elementum3D with Elementum 3D’s aluminum metal matrix composite (MMC) product — A1000-RAM10. Masten’s chamber fires successfully for two reasons, its innovative design and because it is printed out of our A1000-RAM10 product, allowing for the much-desired material that combines lightweight aluminum with the high temperature performance of ceramic.NASA plans to fly repeated trips to the moon with the rocket engine, in rapid sequence with little delay between launches.In addition, we were featured in its 27th episode, Lighter, Better-Performing Brake Rotor From 3D Printing: The Cool Parts Show #27. It was originally broadcasted live and centered around Ceramic Disc Technology for a Dodge Challenger Hellcat. See how Elementum 3D and Ceramic Disk Technologies (CDT Rotors) combined their revolutionary technologies to eliminate two-thirds of the rotor’s mass, deliver five times the thermal conductivity and reduce brake dust by 95% compared to the car’s standard rotor.
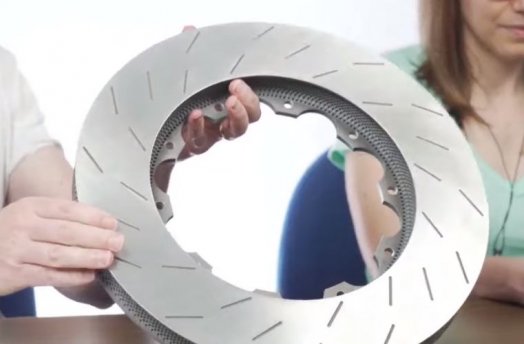
In addition, we were featured in its 27th episode, Lighter, Better-Performing Brake Rotor From 3D Printing: The Cool Parts Show #27. It was originally broadcasted live and centered around Ceramic Disc Technology for a Dodge Challenger Hellcat. See how Elementum 3D and Ceramic Disk Technologies (CDT Rotors) combined their revolutionary technologies to eliminate two-thirds of the rotor’s mass, deliver five times the thermal conductivity and reduce brake dust by 95% compared to the car’s standard rotor.

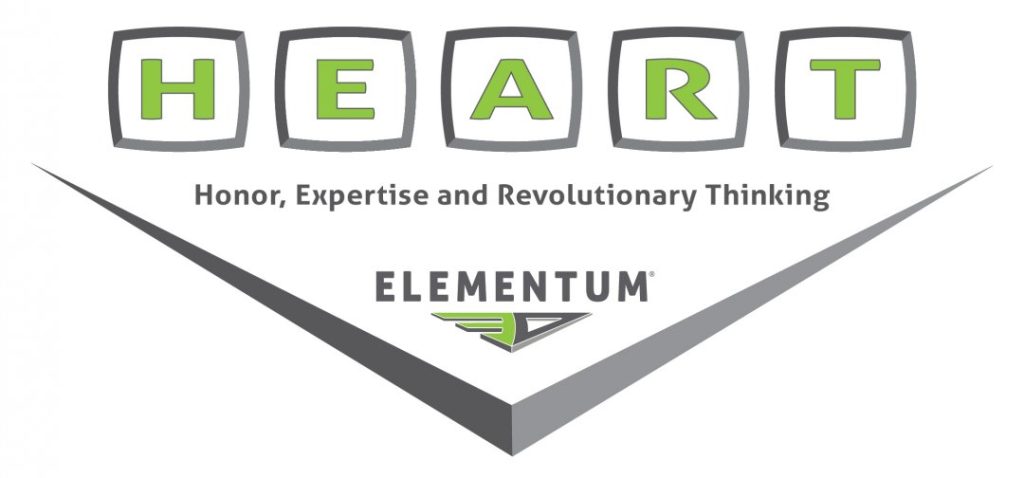
o serve our customers with world-class products and services, we recognize that it starts with our values, norms, attitudes, and beliefs. Recently, senior management established three core E3D values: Honor, Expertise and Revolutionary (AKA “The HEART of E3D”), to publicly set a precedent for excellence.
Establishing a value system that is H.E.A.R.T centered will house the right overarching leadership behaviors and actions to support our customers lofty goals. Collectively, Elementum 3D team members have a clear understanding of who we are and what we stand for in order to inspire the end user to greater achievement in additive manufacturing (AM) with long-term, sustained success.
Now that we have solidified our three core corporate values, let’s break each value down to understand how they directly impact our interactions with the AM community.
Honor
Building our culture based on high respect, high moral standards of behavior starts from within. We recognize that a unified, deeply committed, and interconnected team will form a company that will be forever known as a caring, authentic, and ethical organization that can be trusted.
Expertise
Elementum 3D was founded on educating our customers. We are dedicated to help solve their problems or at least narrow the options by asking in-depth questions and providing relevant data to point them towards a solution that is in the customer’s best interest.
Revolutionary
This vital corporate value identifies us as the leader in metal AM materials development, moreover, it signifies two truths to the entire manufacturing industry: 1. E3D is a stable and reliable entity and 2. Our tireless pursuit to revolutionary thinking brings to market the availability high-quality groundbreaking products and services enabling end-users to reap the design freedoms of additive manufacturing.
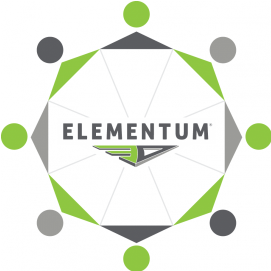
Employee update
Q2 2021 NEW HIRES
Mitchell Kwan – Quality Analyst
Laura Blau – Intern Engineering
David Borum – AM Technician
Gabriel Moreno – AM Technician

- Biden Administration Boosts Support for Additive Manufacturing
- Eye on Innovation: Norfolk Naval Shipyard Participates in Innovative HACKtheMACHINE Challenge
- First Critical Jet Engine Part Made with Metal 3D Printing Receives Air Force Approval
- GE cuts costs by 35% in move from casting to 3D printing technology
- USMC uses additive manufacturing to create vehicle maintenance tool