One of the many considerations in 3D printing is what materials should be used for the printing process. Though still limited, 3D printing materials have expanded in recent years. Going from traditional materials like plastics and polymers, like PEEK and PLA, to metals and composites, there have been huge advancements in the field. Recently, researchers have even found ways to print with previously unavailable materials like copper and bone. However, despite this growth, there is still a long way to go. We were able to sit down with Dr. Jacob Nuechterlein of Elementum 3D, an American an additive manufacturing research and development company that specializes in the creation of advanced metals, composites, and ceramics. We learned about their RAM technology and the metal AM sector!
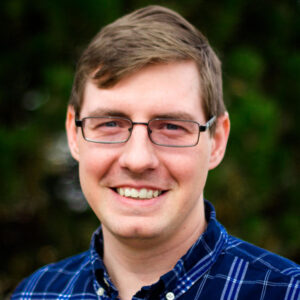
3DN: Could you introduce yourself? When did you start working with 3D printing technologies?
Jacob Nuechterlein, President and founder of Elementum 3D. My background is in materials science and powder metallurgy. I didn’t really work with 3D printing until after I started the company in 2014. In a short time, my company has become one of the world leaders in 3D printing which demonstrates that the industry is moving quickly and new experts in the field are made every day.
3DN: How was Elementum3D formed? What is Elementum3D’s mission?
I raised a small amount of money to get the company off the ground with a mentor of mine, Quinton Hennigh. I started in a corner of a warehouse developing materials on a laser engraver I modified to be able to print in three dimensions. Shortly after filing patents I expanded and added staff to the organization and acquired our first laser powder bed (LPB) 3D printer from EOS. We’ve been developing new materials for LPB ever since.
3DN: Can you tell us a bit more about your RAM technology?
RAM or Reactive Additive Manufacturing forms microstructure controlling precipitates in-situ during the printing process. We use this technology to enable printability of materials that were thought impossible. It also allows us to develop materials specifically for additive manufacturing like our metal matrix composites. While RAM is our core technology it is not our only materials development tool at Elementum 3D.
3DN: What are the needs of the AM community in terms of AM metals? How is Elementum3D meeting these needs?
Additive manufacturing has a limited selection of materials capable of meeting specific property requirements. Three key areas we are frequently asked about are thermal conductivity, high temperature performance, and high strength. Recently we have developed materials for elevated temperature applications. We have aluminums that operate at 200 C higher temperature than cast aluminum alloys. We also recently released nickel superalloys that operate at temperatures well over IN718 (the standard in the industry). We also offer a wide range of materials for applications including radio frequency devices, engine blocks, and thermal management for server farms
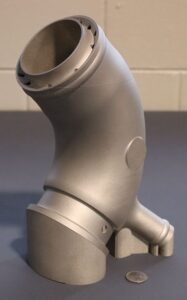
3DN: More globally, what are some of the barriers to creating quality materials for the metal AM process?
New customer adoption of AM in general is a first barrier to development. This restricts funding for technological innovations which are complex and require expensive and iterative testing. Another major barrier for adoption is the lack of a global set of international standards for testing. This creates multiple hurdles and repeat expenses to adhere to individual requirements from each customer. Moreover, during the printing process the material microstructure forms which can affect the consistency if the process is not well controlled. This can be exasperated if the process window of the specific material is too tight.
3DN: Who are the main users of metal AM today? (Sectors, products, etc.)
Aerospace, space, defense, medical, high-end automotive, thermal management, energy, oil and gas and others are all using additive manufacturing to some degree. Space and defense sectors seem to be the fastest to adopt additive manufacturing due to logistical and space saving business cases. Many companies have been able to demonstrate business cases where additive manufacturing can compete with CNC machining.
3DN: How do you believe the AM metals sector will evolve in the next 5 years?
I expect to see significant growth in flexible manufacturing spaces that can be ramped rapidly and help reduce warehouse space for spares. As companies demonstrate the ability to replace traditionally machined parts with additive the logistical benefits begin to outweigh the risk of a new manufacturing method. Recent advancements to increase printing speed, and therefore lower costs, have opened many new applications, but the materials selection and lack of data has held adoption back.
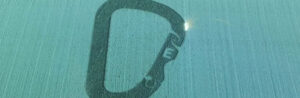
3DN: Any final words you would like to share with our readers?
Additive is on the brink of growing exponentially and we will need high quality materials along with more options to continue moving the industry forward. 3D printing has replaced other manufacturing in several applications and companies who are not considering printing today are already behind the curve. You can find out more about Elementum 3D HERE.