Why are metal AM powders critical to quality printed parts?
Why are metal AM powders critical to quality printed parts?
In this issue of Tech Talk Ben Rafferty, Elementum 3D materials engineer, will discuss powder selection, the first
and perhaps most important step in the additive manufacturing (AM) process. He’ll be covering key attributes of
quality metal AM powder including size, shape (morphology), flowability, tap density, and composition. These
characteristics all contribute to achieve a high quality AM part.
Most people are not aware of metals three-dimensional printing and the extent that you can print complex high
performance parts. When I started my career as a material engineer, I was only aware that printing metal was an
emerging option; it wasn’t until I started working with Elementum 3D that I saw how important metal powders
designed specifically for additive manufacturing (AM) are to the performance of printed metal parts. Additive
manufacturing involves the addition of material to produce parts directly from a computer model, as opposed to
a subtractive machining process that removes material to produce a part. Laser Powder Bed Fusion (L-PBF) is an
industrial AM process that produces complex near net shape parts with near full theoretical density. Properties
often exceed cast parts and may approach or even exceed forged/wrought parts.
POWDER SIZE
It is important to use a powder particle size range that produces good flow or spreadability while also producing
a uniform melt pool with good surface finish. Particles that are too big may not fully melt and result in interstistial
voids remaining in the part. If the particles are too small, the powder may not flow and spread well and may
result in excessive material ejected and vaporized from the melt pool. The powder must also perform consistently
over thousands of layers and many re-uses. A common size range for L-PBF powder is 15-45μm, but the
preferred distribution depends on the material that is being printed and the feed and spreading system of the
printer. A material with a higher theoretical maximum density may use a smaller size distribution while a lighter
metal may need larger particles to improve consolidation and reduce the chance of being blown by the inert gas
stream. Other powder characteristics including shape and surface also affect the size range that will work best
with the powder. Cost is also a factor since most production methods produce a range of particle sizes and so
cost is reduced if a larger range can be used.
SHAPE
In addition to controlled size range, the particle morphology is also important for AM powder. The most desirable shape for AM is a sphere. Spherical particles will enable the powder to stack and flow optimally during the LPBF
process.
This spherical shape is typically achieved during powder production by gas or plasma atomization or plasma spheroidization. In gas atomization, material is melted and made into droplets through one of several methods which then solidify in relatively spherical form due to surface tension. Plasma spheroidization passes material feed stock that is already in particulate form through a plasma in an inert chamber to partially or fully re-melt the particulates and produce highly spherical products with relatively smooth surfaces. The powdered metal that is produced is then classified for size typically by screening or cyclone classification. Finer and larger particles may be used for other processes or may be able to be re-melted for re-atomization. The powder surface roughness is also an important characteristic and will have a significant effect on flow. A smooth surface will increase powder flow compared to a rough surface. Satellite particles, which are smaller particles fused to larger particles, are also detrimental to flow. Hollow particles can result in porosity in the part and are therefore also typically detrimental.
As powder is reused, the fraction of smaller particles may be reduced as a result of the fine particles settling out during recoating and being incorporated into the part. This may improve the flow of the powder over time as some of the small particles that impede the flow are used. A steady state is typically reached where the material used in the part or fused and sieved out is balanced by fresh material added to the feed stock replace it after the build. Figure 3 shows an example of virgin power and reused powder with the reused powder showing fewer small particles.
Spherical shapes are key to creating a more efficient packing structure to increase the tap density, resulting in fully dense parts with a superior surface finish. Figure 4 shows examples of several powder morphologies common in AM. The spherical characteristic of the powder is needed to achieve good part feature definition and minimize pores, cracks, inclusions, and surface roughness for the final part. It is also very important for achieving consistent key bulk powder properties such as packing density and flowability.
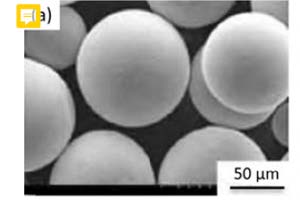
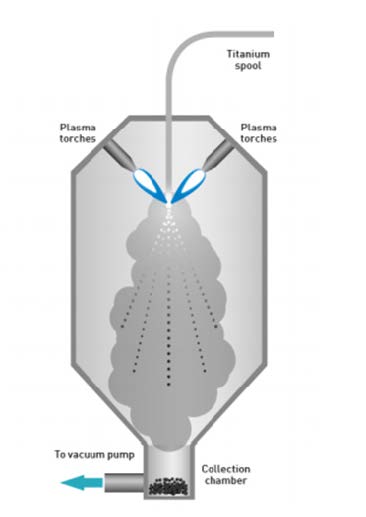
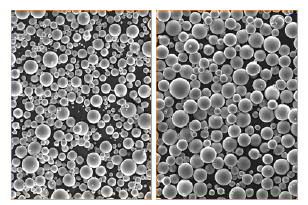
FLOWABILITY
Flowability and spreadability are qualitative properties that depend on powder composition, size, morphology, surface roughness, and moisture content. Uniform flow is required across the build substrate layer after layer to achieve good feature definition, part density, and surface quality. Particles that have satellites or a rough surface will increase the friction between particles and impede the flow of the powder. Irregularly shaped particles impede powder flow due to steric interference, resulting in an AM part with increased porosity, decreased density and rough surfaces. Moisture content can play a critical role in powder behavior and it is important to keep power dry for optimal performance. Electrostatic effects can also have a significant influence over powder behavior at small particle sizes.
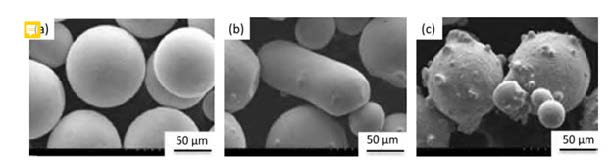
Powder behavior and flowability can be evaluated by ASTM standards for bulk and tap density (B527), Hall funnel (B213), Carney funnel (B964), rheology testing equipment, and by the angle of repose. Tap density is performed by taking a known mass of powder, pouring it into a graduated cylinder and repeatably tapping the bottom until the powder has settled. According to ASTM B527-15, refractories need approximately 3000 taps. For example, we have found that our tungsten has a tap density 10.00g/cm3 compared to 19.3g/cm3 the theoretical density of the material as a solid. The difference in the density shows that approximately 48% of the volume of the tapped powder is open space (air) between particles.
A spreadable powder that flows across a build surface in laser powder bed fusion is necessary to deposit a suitable layer over the build surface to produce high quality parts. The fact that metal powders come in all shapes and sizes is why it is important to be able to characterize your powders.
POWDER COMPOSITION
Powder composition is a key factor to produce parts with the desired properties. In addition, small changes to powder composition can affect porosity, microstructure, microcracking, and macrocracking. According to Jean-Pierre Kruth, due to the high melting temperatures and the fast-thermal cycles of L-PBF, stress cracking is a common concern for many materials. Starting with the correct composition, particle size, and shape will allow the material to wet consistently. The ideal wetting situation is a flat droplet with an angle less than 90° to the weld surface. If there is an insufficient wetting of the material a balling effect will occur causing porosity and effecting the bulk mechanical properties. Compositional changes can have a significant effect on surface tension and melt viscosity which affect balling behavior in the melt pool.
Oxidation and moisture control in the feed stock is important to provide the correct properties of the powder and the printed part. Having a stable material is essential for powder reuse because oxygen and moisture impurities can increase with reuse and result in altered properties. According to additive manufacturing of metallic components, the effects of oxygen in the powder AlSi10Mg during the printing process can reduce the yield strength and it was shown that oxygen concentrations below 0.027wt% result in high yield strengths for aluminum. [6] Oxygen also has a large influence in the printing of Ti64, with oxygen causing the tensile strength to increase but the elongation and toughness to decrease. [7] For this reason, there is a need to control the powder environment to consistently produce high quality AM products.
CONCLUSION
It is important to choose the correct powder for your AM process. First, determine what material properties are needed for your part and choose the appropriate material type to meet these needs. Second, choose a powder with sufficient flow, spreadability, and particle size for your AM system. Finally, choose a powder with characterized printed part performance data for your process to be sure that the powder feed stock will actually produce the properties you need when used in a commercial AM system.
Please contact us for additional information at www.elementum3d.com
References
[1] Malvern Instruments Limited, “Optimizing metal powders for additive,” Malvern Instruments Limited,
Worcestershire, 2017.
[2] *. N. O. B. V. K. L. L. T. Aljaž Ivekovića, “Selective laser melting of tungsten and tungsten alloys,” International
Journal of Refractory Metals, vol. 72, pp. 27-32, 2017.
[3] ReniShaw Lucy Grainger, “Investigating the effects of multiple powder re-use cycles in AM,” ReniShaw,
Wotton-under-Edge, 2018.
[4] b. D. a. M. a. S. a. T. a. Qimin Shi a, “Effects of laser processing parameters on thermal behavior and
melting/solidification mechanism during selective laser melting of TiC/Inconel718composites,” Optics and laser
Technology, vol. 84, pp. 9-22, 2016.
[5] J. Deffley and . R. Clayton, “Optimising metal powder for additive manufacturing,” metal-powder.net, no. 26,
pp. 14-17, 2014.
[6] T. DebRoy, H. L. Wei, J. S. Zuback, T. Mukherjee, J. W. Elmer, J. 0. Milewski, A. M. Beese, A. Wilson-Heid, De, A.
De and W. Zhang, “Additive manufacturing of metallic components – Process, structure, and properties,”
Progress in Materials Science, vol. 92, pp. 112-224, 2017.
[7] J. Dawes, R. Bowerman and R. Trepleton, “Introduction to the Additive Manufacturing Powder Metallurgy
Supply Chain,” Johnson Matthey Techonolgy, vol. 59, p. 2