Powder Recycling White Paper: Improving Processing, Maintaining Quality
Powder Recycling in Laser Powder Bed Fusion: Improving Processing, Maintaining Quality
At Elementum 3D, we aim to provide a quality product with our customers’ interests and needs in mind. The introduction of our Reactive Additive Manufacturing (RAM) technology has allowed for a wide variety of materials systems that have not been printable by laser powder bed fusion (L-PBF) to now be commercially available. Along with bringing new materials to the market the RAM technology has shown to have equivalent and improved mechanical properties when compared to traditional wrought alloys. This technology utilizes micron-scale additives blended into our powder feedstock that react in situ during printing to form sub-micron inoculants. These inoculants lead to grain refinement and contribute to the elimination of defects like hot tearing in aluminum, a hurdle for many alloys in AM. Elementum 3D’s uniquely designed alloy feedstock for laser powder bed fusion (L-PBF) has been found to generate light weight, high strength, AM parts. With these specialty powders an area of interest for many consumers is the utilization of powder for multiple builds, or powder recycling. To consider this possibility with our material, studies were performed on three of our different RAM materials.
Benefits and Challenges of Powder Recycling
Powder recycling is both economically and environmentally beneficial, as it increases the amount of builds performed with the same feed stock, as well as reduces the amount of material wasted per build. Additionally, powder processing allows for blending of multiple components, for production of materials like metal matrix composites (MMCs). However, there is some concern regarding physical and chemical changes that could occur due to processing conditions in L-PBF as well as segregation of components in the powder during handling. The layer-by-layer building process inherent to L-PBF causes thermal cycling that can lead to loss in chemical composition [1]. It has also been found that changes in particle morphology can lead to variances in mechanical behavior [2], while changes in particle size distribution can affect flowability and lead to inhomogeneous powder distribution over the build platform [3]. Improper powder handling can expose powders to moisture in humid environments, which can oxidize particle surfaces or induce impurities, altering the mechanical performance of a part [4]. There is also concern regarding segregation during handling of powder feedstock due to differences in powder size and relative density [5-6]. Despite these concerns, many alloys have been found to retain chemistry, particle size, morphology, and mechanical properties after multiple builds with the same powder [2-3]. Additionally, powder processing has been found to provide improved homogeneity in multi-component materials (e.g. MMCs) versus liquid processing, where dendritic solidification and agglomeration of added particles encourages segregation [7].
Our Materials, The RAM Advantage
Considering the factors outlined above, we wanted to ensure our material could provide the benefits of powder recycling, while still maintaining the quality we promise to our customers. Using three different studies of our A6061-RAM2, A2024-RAM2, and IN625-RAM2 materials, respectively, we were able to confirm that our material stood up to the challenge. This technique also allows for larger, safer particle sizes, for storing and handling that form the beneficial sub-micron reinforcement during the printing process.
Powder Segregation Study A6061-RAM2
Pushing the limits of our material, we decided to emulate a “worst-case scenario” of segregation of particle constituents in an experiment with our A6061-RAM2 material. In a mixture, particles with relatively higher density and smaller size tend to settle to the bottom of a container with time or movement [5-6]. For instance, considering a jar full of various sizes of material, such as sand, pebbles, and rocks, the finer material, sand, would tend to settle to the bottom while the larger material, pebbles and rocks, would stay relatively in the same place. While our multicomponent powder mixtures aim to minimize this phenomenon by using similar size matrix and additive particle sizes and relative densities, we wanted to ensure segregation was not occurring after multiple handling cycles and builds. To achieve this, used powder was taken from a build and sieved 20 times consecutively with no re-blending. In this sieving process, the powder was consistently fed into the sieve from the bottom of a collection bin to maximize potential segregation between various components in the powder that may tend to settle to the bottom versus the top of the bin (Figure 1). Two additional prints were then performed, one using the top and another the bottom half of the powder in the bin, followed by evaluation using tensile testing. The results shown in Figure 2 display the consistency of performance in our powder, even in a “worst-case scenario” of handling that could encourage component segregation in the reused powder.
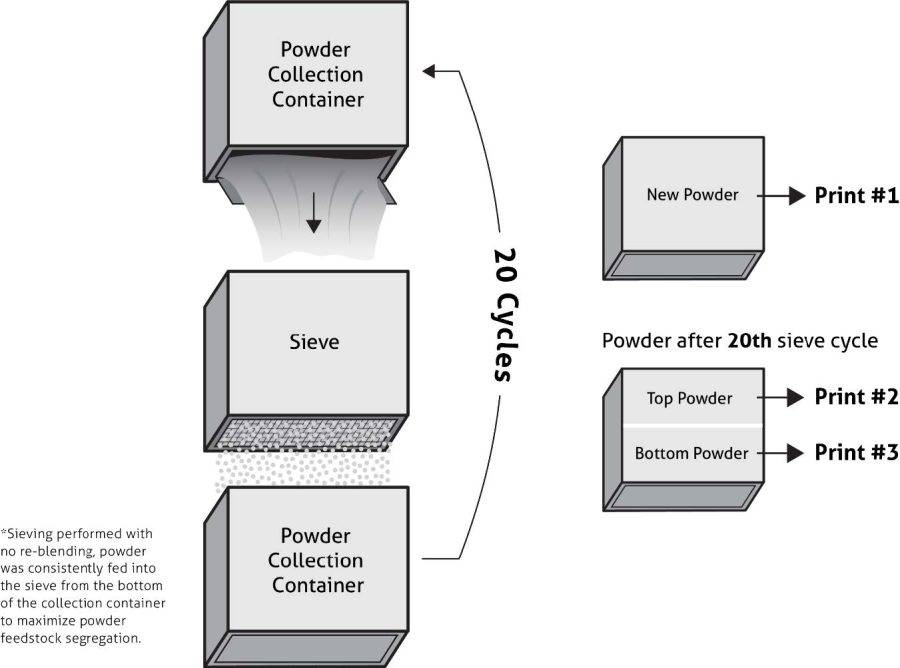
Consistency of Particle Chemistry and Size Distribution in A2024-RAM2
With a development partner, we also ensured maintenance of particle size and chemistry after multiple builds in an SLM 280 printer outfitted with a powder supply unit (PSV). After multiple builds using our A2024-RAM2 powder over a period of 5 months, and 70 cycles of sieving without refreshing with new powder, our material was found to have a similar particle size range as the new powder and preserve chemistry that was in-spec (Figure 3). This confirmed that our material not only achieves consistent strength values, but also remains well mixed with the same particle characteristics as new powder.
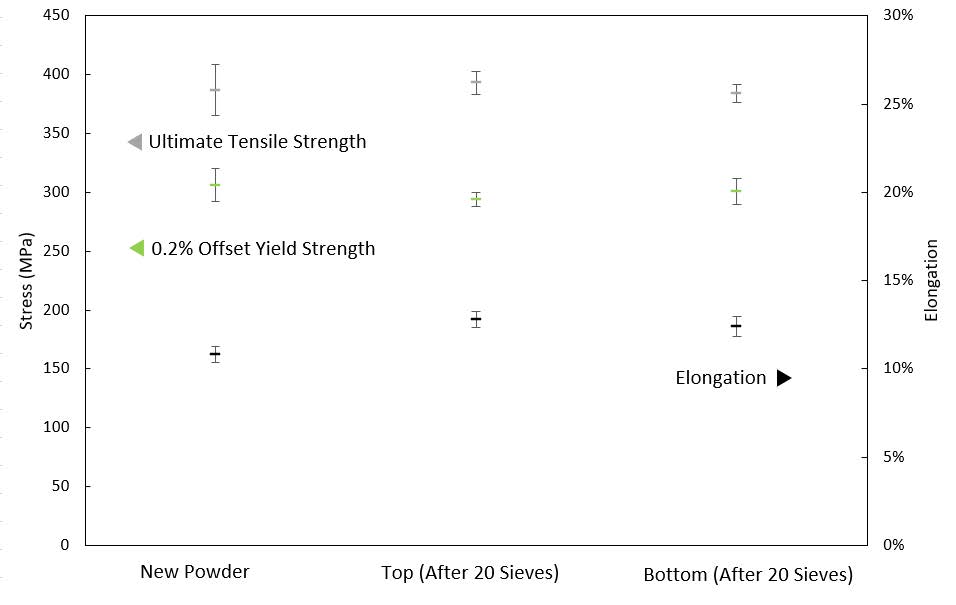
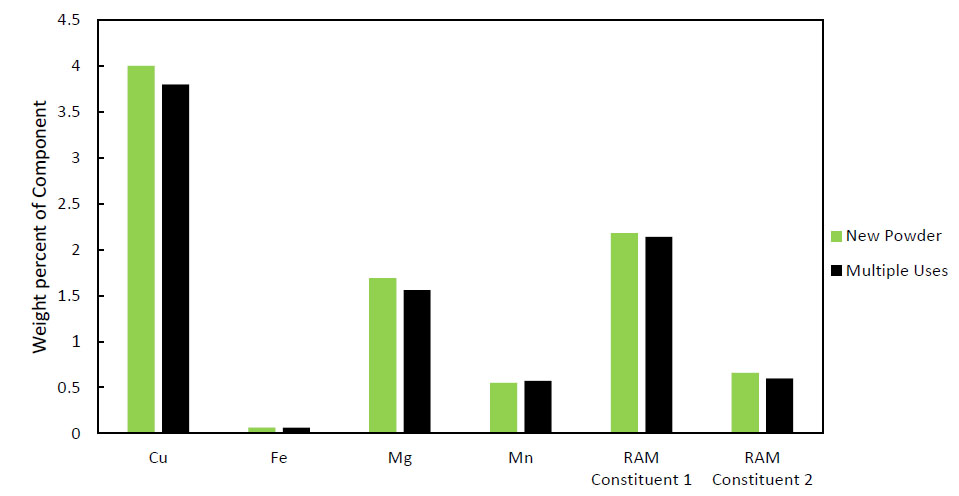
Retaining Mechanical Performance in IN625-RAM2
In a study performed by a team of students at Colorado School of Mines (CSM), our Inconel 625 nickel alloy with 2% ceramic reinforcements (IN625-RAM2) was evaluated based on tensile properties of bars and impact energy of Charpy specimens printed with recycled powder. Following a first build printed with new powder (labeled 0 in the figures below), the used powder was topped off with additional new powder to maintain an amount of 25 kg for each build and tumbled for 10 minutes to ensure proper mixing. This was done for each build up to 9 builds (or 8 reuses), each of which was performed on an EOS M290 L-PBF printer at Elementum 3D. The resulting tensile properties of bars taken from the 1st, 2nd, and 8th reuse (2nd, 3rd, and final build) in Figure 4 and 5 show consistent strength values above 1225 MPa for ultimate tensile strength (UTS) and 850 MPa for yield strength (YS), both of which are higher than those reported for wrought plate of the same material according to the manufacturer’s data sheet (827-1103 MPa for UTS and 414-758 MPa for YS) [8]. The Charpy specimens were also found to have a similar impact energy (Figure 6) up to the final 8th reuse. These results indicate not only the resilience of our material over multiple builds, but also our capability to out-perform other manufacturing techniques with our material and methods.
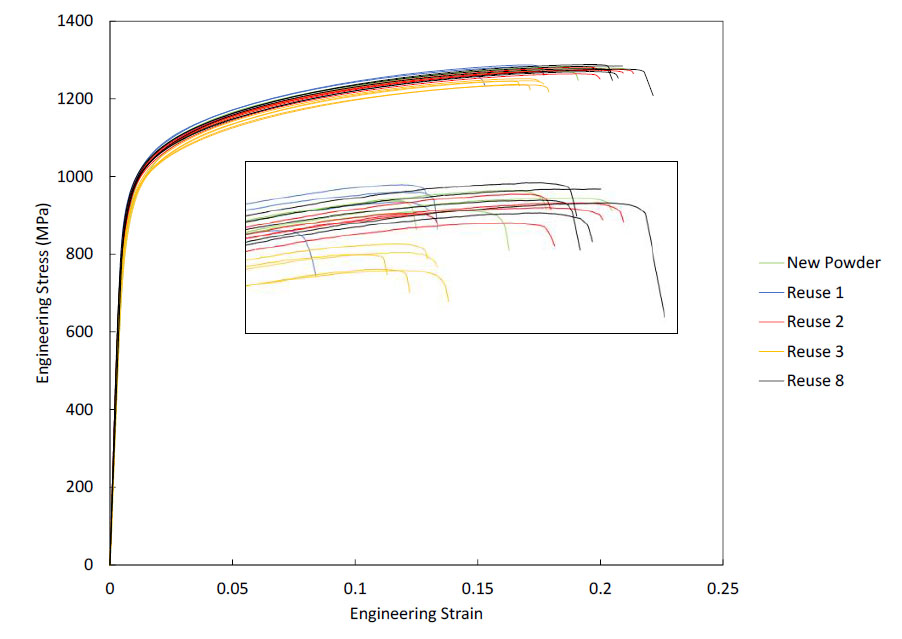
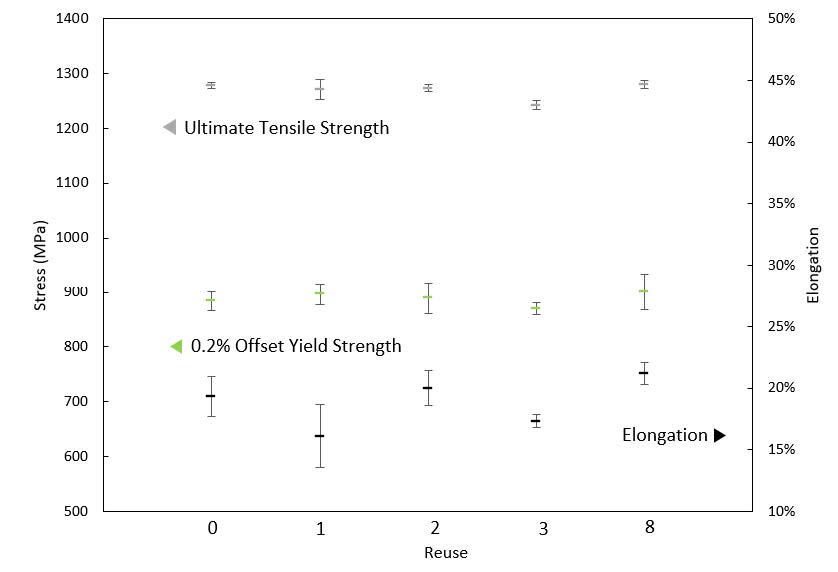
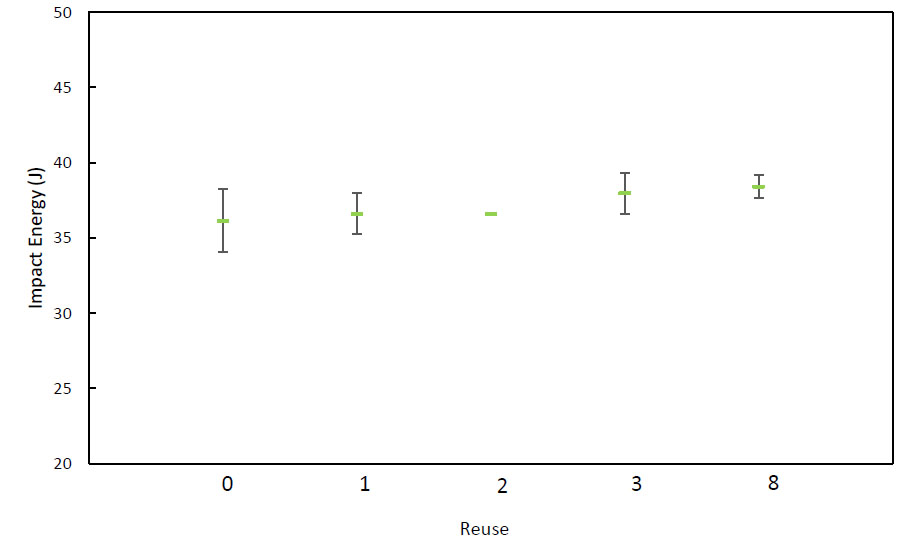
Investing in a Sustainable Future with a Quality Product
Each of the above studies helped us to explore and confirm the quality and performance of our powder feedstock material over multiple builds. The resulting consistency of mechanical properties and powder characteristics in these studies help us to assure our customers of the resilience and reliability of our unique powder feedstock materials. The reusability of our powder stems from the reactive powder design, which allows for use of micron-scale reactive powders to achieve sub-micron products that act as grain refiners. The similar size and relative density of these additions and our matrix alloy powder prevent segregation from occurring even after multiple cycles of powder handling and sieving. The reactive process of our RAM material, which consists of dissolution of our reactive additives in the melt and reprecipitation of the products as sub-micron inoculants, that occurs during printing also encourages homogeneity of these constituents in the final product. With these results we hope to showcase the economic value and sustainability of our product, as well as our commitment to providing quality solutions to our clients.
For additional information contact: Anthony@elementum3d.com or jacob@elementum3d.com
References
[1] F. H. Froes, Additive manufacturing for aerospace applications-part I, Advanced Materials and Processes (July/August) (2017) 36-40.
[2] H. Asgari, C. Baxter, K. Hosseinkhani, M. Mohammadi, On microstructure and mechanical properties of additively manufactured AlSi10Mg_200C using recycled powder, Materials Science and Engineering A 707 (2017) 148-158.
[3] L. C. Ardila, F. Garciandia, J. B. Gonzalez-Diaz, P. Alvarez, A. Echeverria, M.M. Petite, R. Deffley, J. Ochoa, Effect of IN718 recycled powder reuse on properties of parts manufactured by means of Selective Laser Melting, Physics Procedia 56 (2014) 99-107.
[4] A. Das, J. A. Muniz-Lerma, E. R. L. Espiritu, A. Nommeots-Nomm, K. Waters, M. Brochu, Contribution of cellulosic fibre filter on atmosphere moisture content in laser powder bed fusion additive manufacturing, Scientific Reports 9 (2019).
[5] Z. Wang, M. Song, C. Sun, Y. He, Effects of particle size and distribution on the mechanical properties of SiC reinforced Al-Cu alloy composites, Materials Science and Engineering A 528 (2011) 1131-1137.
[6] M. J. Tan, X. Zhang, Powder metal matrix composites: selection and processing, Materials Science and Engineering A244 (1998) 80-85.
[7] S.F. Moustafa, Z. Abdel-Hamid, A.M. Abd-Elhay, Copper matrix SiC and Al2O3 particulate composites by powder metallurgy technique, Materials Letters 53 (2002) 244-249.
[8] Special Metals Corp., INCONEL alloy 625, Tech. rep. (2013). doi: SMC-066.